October 2015
The Mountain arrives
30/10/15 21:30
We knew that the volume of material Pegasus, the external insulation system installers, would use was large but seeing the first delivery fill up about half of the volume of the ground floor was still a shock. Another delivery of material is scheduled for next Wednesday by which time most of Friday's material will be installed on the gable wall. Progress will then be slowed down by the need to readjust the scaffolding before the insulation can be applied to the rear walls. Liam and Glenys provide scale in the photo below. the boxes behind Liam contain the mechanical fixings for the 300mm Graphite EPS.
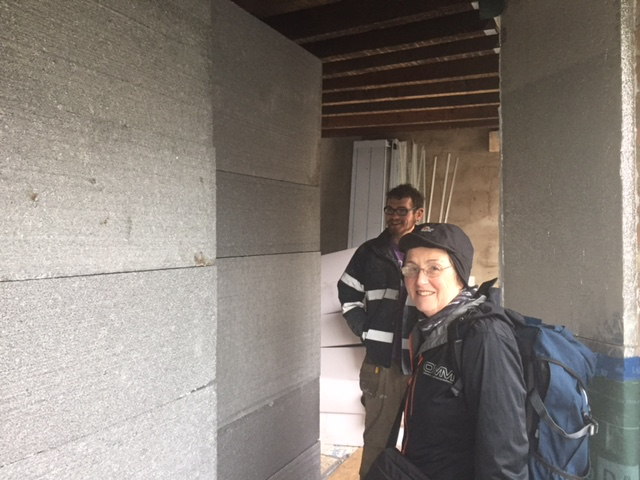
I was pleasantly surprised by the thermal conductivity λ=0.030W/mK - I was expecting a rating of λ=0.032W/mK. This 'small' difference drops the annual heating demand by 44kWh. Yesterday I looked at the VIP panel labels that have been waiting installation for several weeks and was again pleased by the lower than expected rated thermal conductivity. Some months ago I had spent a long time searching for the CE rated U value on the internet without success. The figure I had been using in the PHPP software was 0.0077W/mK which was an aged value supplied by the supplier. The 'correct' figure of 0.0066W/mK which made a saving of over 60kWh/a.
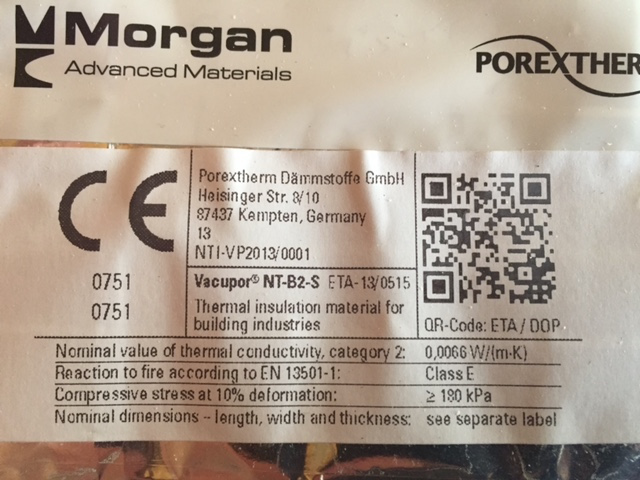
I am anxious to make the most of the Kingspan offcuts and this also reduces costs by reducing the number of skips required. The offcuts are being used to good effect in the weaker areas of the roof space - over the tops of the walls at the rear of the property and the valley between the two roof planes - where the specified fill of 750mm Warmcell 300 cannot take place. Of course the critical areas are the most difficult to reach but Henry doesn't seem to mind.
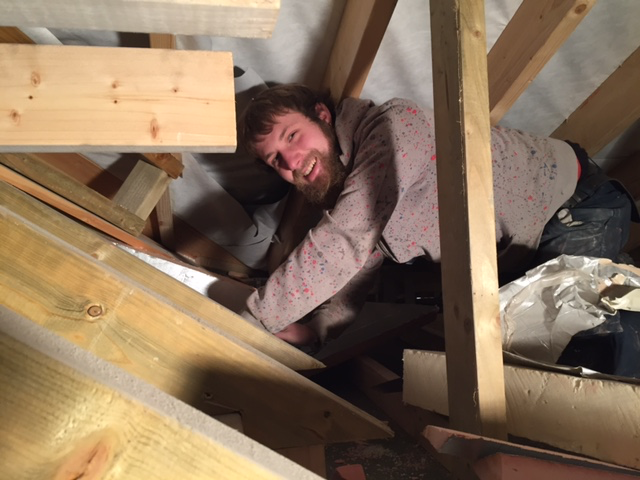
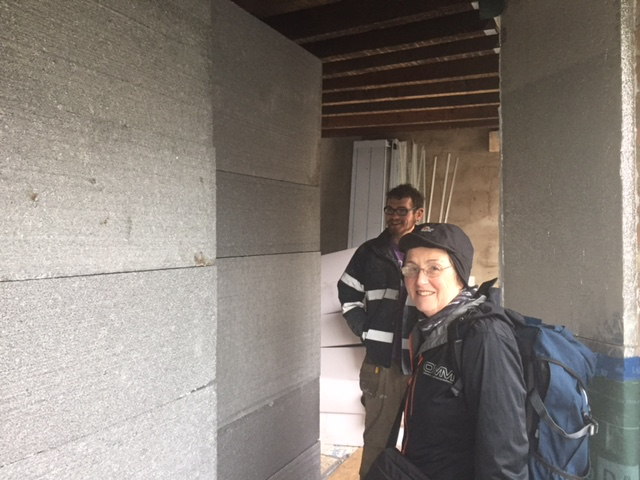
I was pleasantly surprised by the thermal conductivity λ=0.030W/mK - I was expecting a rating of λ=0.032W/mK. This 'small' difference drops the annual heating demand by 44kWh. Yesterday I looked at the VIP panel labels that have been waiting installation for several weeks and was again pleased by the lower than expected rated thermal conductivity. Some months ago I had spent a long time searching for the CE rated U value on the internet without success. The figure I had been using in the PHPP software was 0.0077W/mK which was an aged value supplied by the supplier. The 'correct' figure of 0.0066W/mK which made a saving of over 60kWh/a.
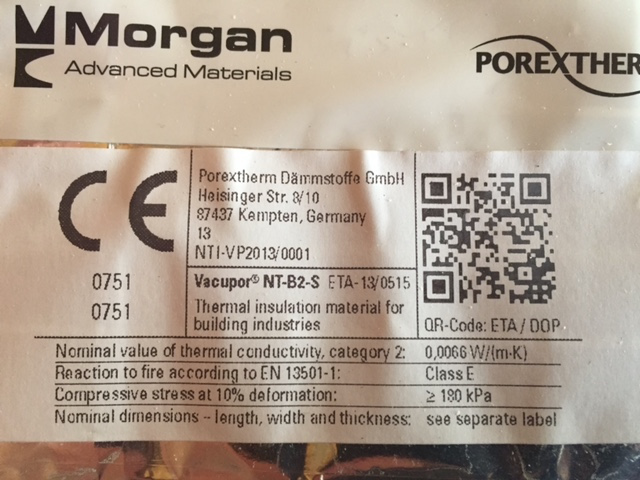
I am anxious to make the most of the Kingspan offcuts and this also reduces costs by reducing the number of skips required. The offcuts are being used to good effect in the weaker areas of the roof space - over the tops of the walls at the rear of the property and the valley between the two roof planes - where the specified fill of 750mm Warmcell 300 cannot take place. Of course the critical areas are the most difficult to reach but Henry doesn't seem to mind.
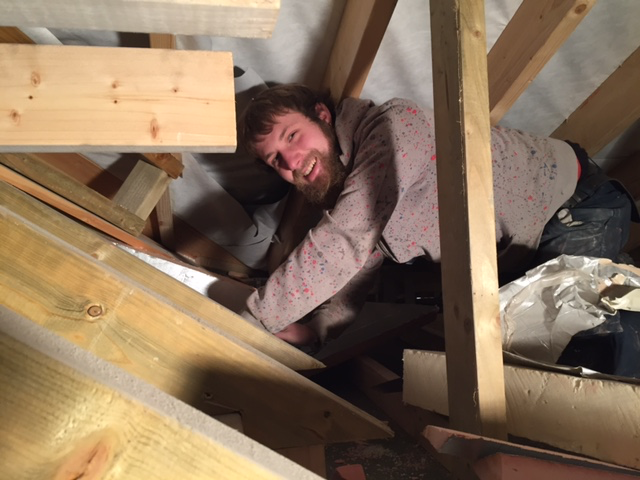
Rapid Progress
28/10/15 21:13
In contrast to the period in early summer when progress seemed very slow things are now visibly changing every day. Liam is devoted to the internal front face of the house and now is working on the Ground Floor. The vacuum insulated panels are proving a challenge because they can't be cut down and he has to work with the sizes available on site. The photo below that he is managing rather well and the area left to the right of the front door will be mostly filled in with the 150mm wide panels
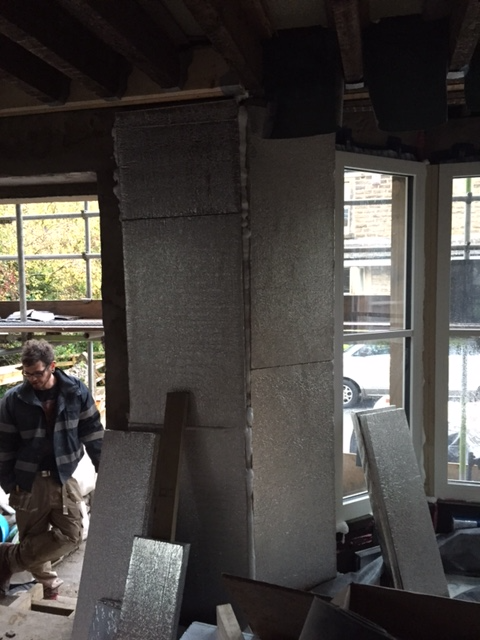
Meanwhile work on the Basement has restarted. It was awaiting the contractors from Electricity North West repositionning the incoming mains and meter position to allow the 'tanking' to be completed. The complication was that before this could be done they had to alter the supply to our neighbour to be direct from the mains cable under the pavement instead of via our basement. So the saga that started in Spring 2014 ended on the 26th October 2015! The photo below shows the old supply pipe to our neighbours - now removed.
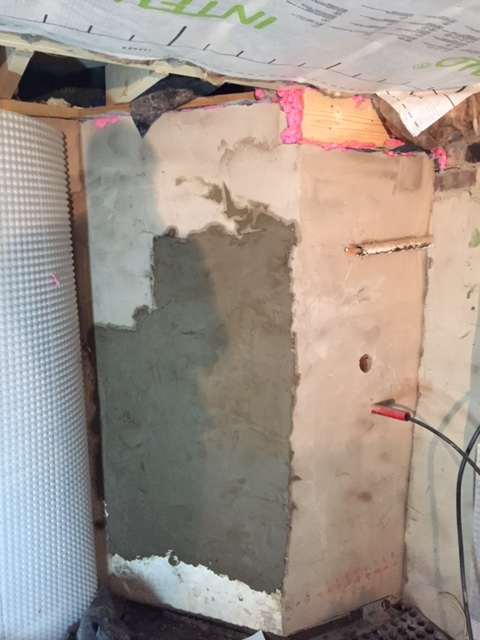
Gideon, the joiner, has been working on the first floor and now all the Vapourboard has been fixed to the ceilings (apart from a panel to allow the loft insulation to be blown in). This allowed the electrician to make his first visit and he took the opportunity to run most of the cable. He was pleased with the service ducts we have for the wiring and plumbing.
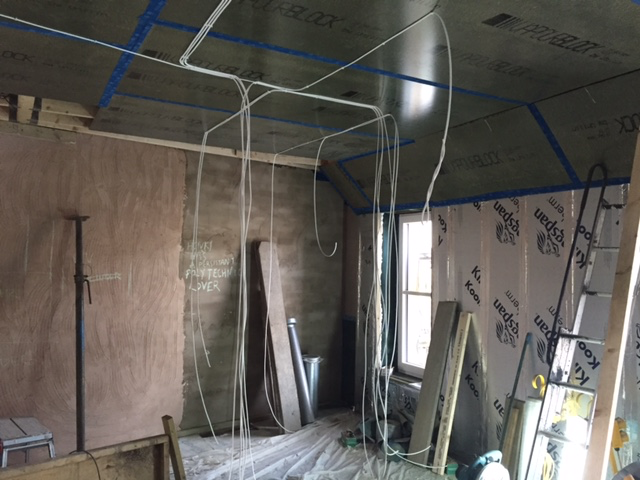
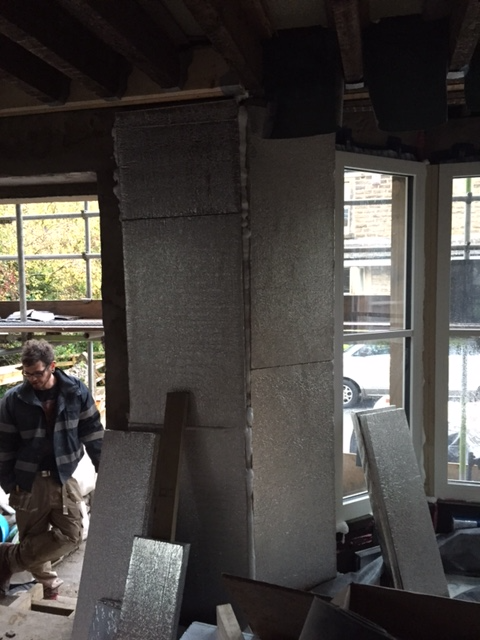
Meanwhile work on the Basement has restarted. It was awaiting the contractors from Electricity North West repositionning the incoming mains and meter position to allow the 'tanking' to be completed. The complication was that before this could be done they had to alter the supply to our neighbour to be direct from the mains cable under the pavement instead of via our basement. So the saga that started in Spring 2014 ended on the 26th October 2015! The photo below shows the old supply pipe to our neighbours - now removed.
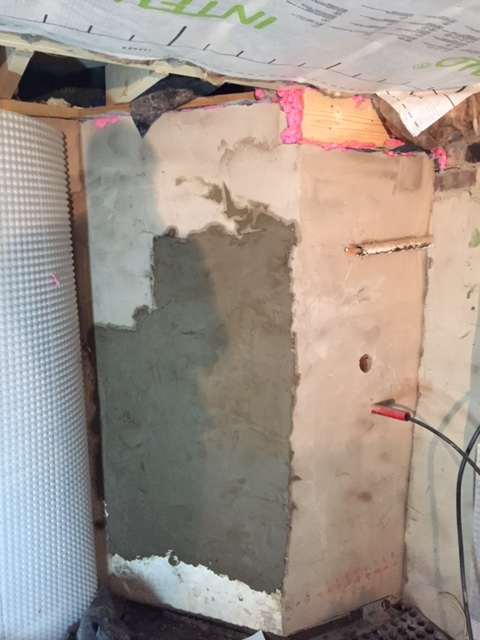
Gideon, the joiner, has been working on the first floor and now all the Vapourboard has been fixed to the ceilings (apart from a panel to allow the loft insulation to be blown in). This allowed the electrician to make his first visit and he took the opportunity to run most of the cable. He was pleased with the service ducts we have for the wiring and plumbing.
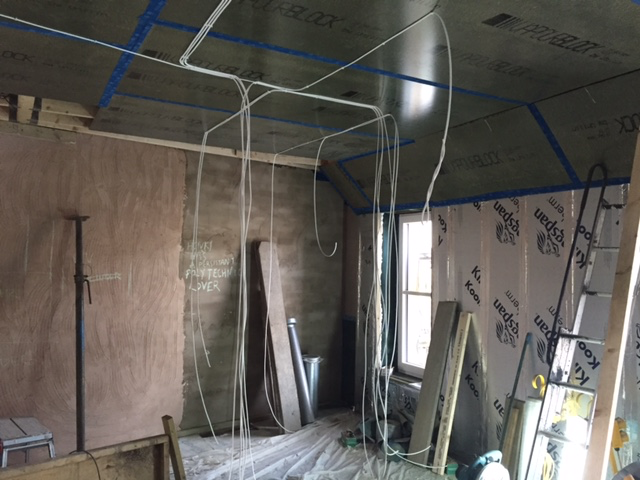
Glenys in cold water?
18/10/15 16:21
The external insulation didn't happen last week but we are hopeful it will start this week. The solar pv panels have also not been fitted because Sundog need the radial circuit installed to the inverter so they can complete all their work in one visit. Given how much work pressure they must be under with the proposed reduction in feed in tariffs I can understand their position.
Work did continue. Gideon (the joiner) was in his element fitting the ceiling joists these are now all installed so the vapour board can now be installed below them which will then permit the stud walls to be fitted.
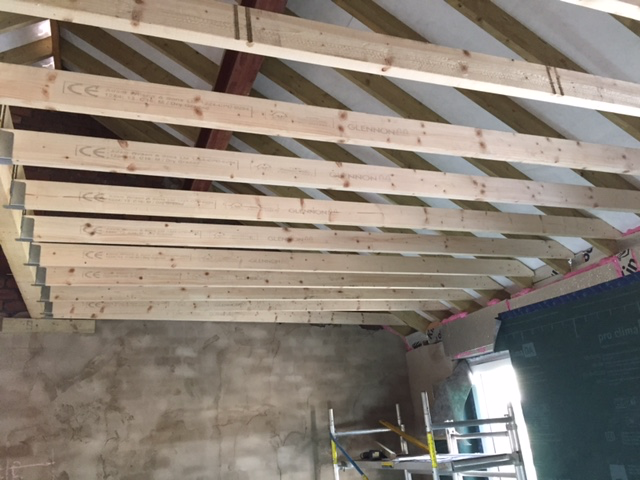
The plasterers have been on site for the last six days and have started on the gable wall. This has proved to be not vertical and not flat so is taking many bags to prepare for the skim coat.
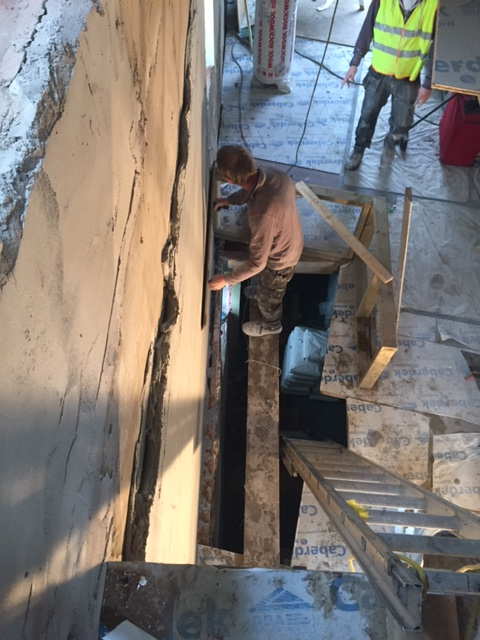
You can see from the photo above that more than the assumed 15mm has been applied to the side of the stairwell. This will require adjustments to the stair widths already supplied to Stairs and More. Having a house with no real reference points to measure from is frustrating.
A warning to anyone planning a new build or attempting a renovation than involves changing the plumbing system - make sure you calculate your demand for hot water rather than simply assume everything will be OK. Look at the new page on Hot Water
Work did continue. Gideon (the joiner) was in his element fitting the ceiling joists these are now all installed so the vapour board can now be installed below them which will then permit the stud walls to be fitted.
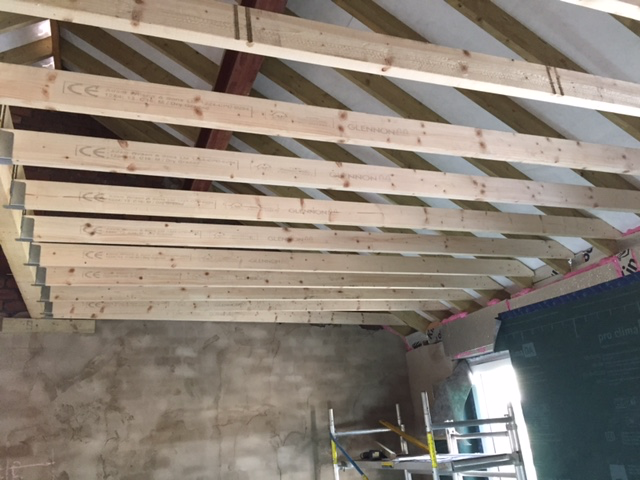
The plasterers have been on site for the last six days and have started on the gable wall. This has proved to be not vertical and not flat so is taking many bags to prepare for the skim coat.
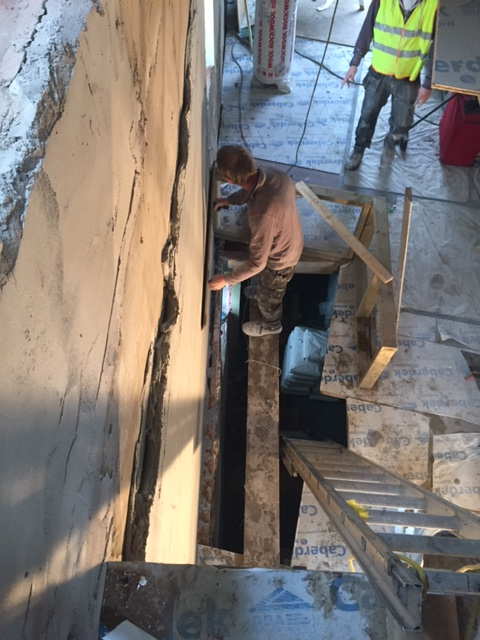
You can see from the photo above that more than the assumed 15mm has been applied to the side of the stairwell. This will require adjustments to the stair widths already supplied to Stairs and More. Having a house with no real reference points to measure from is frustrating.
A warning to anyone planning a new build or attempting a renovation than involves changing the plumbing system - make sure you calculate your demand for hot water rather than simply assume everything will be OK. Look at the new page on Hot Water
Windows are in!
12/10/15 16:46
Ecohaus Internorm fitted all the windows and back door last week in three days. The team of three were very efficient and didn't face any problems with the installation. The building is now a lot less drafty but keeping the window and door in pristine condition will prove challenging on an active building site. The look of the Bay Window was agonised over but the finished result looks similar to the original Victorian sash windows and we are both relieved.
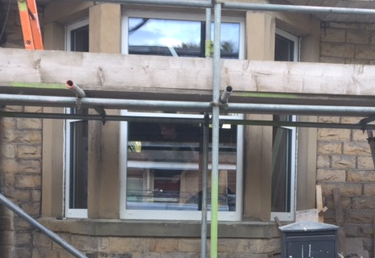
The roofers have finished the slating and we are now ready for Sundog to fit the PV panels. The ridge tiles still need to be fitted and there is some work on the old chimney stack to complete but that shouldn't take long.
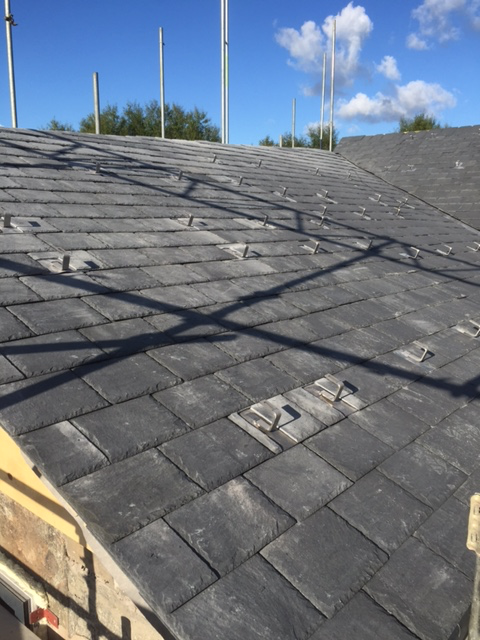
Sundog are hoping to fit this job in between their other projects and they may even turn up tomorrow.
We were expecting a start to be made on installing the external insulation today but that hasn't happened. Given the good weather currently we can't afford this to be delayed much longer.
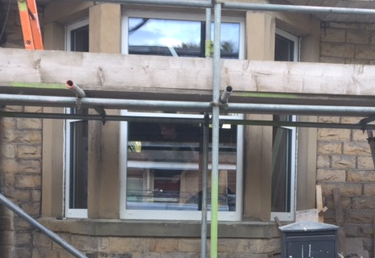
The roofers have finished the slating and we are now ready for Sundog to fit the PV panels. The ridge tiles still need to be fitted and there is some work on the old chimney stack to complete but that shouldn't take long.
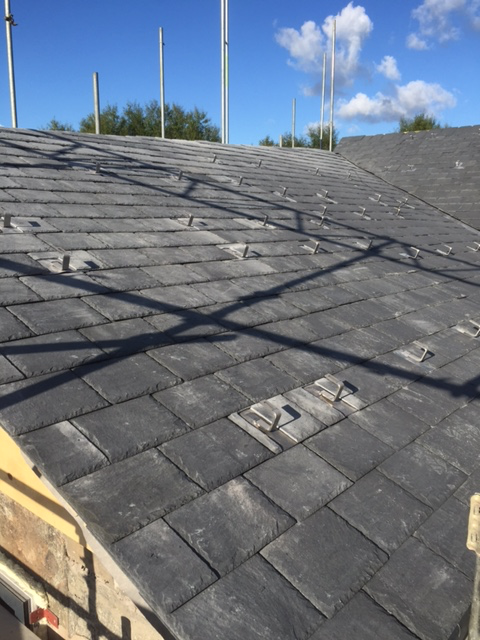
Sundog are hoping to fit this job in between their other projects and they may even turn up tomorrow.
We were expecting a start to be made on installing the external insulation today but that hasn't happened. Given the good weather currently we can't afford this to be delayed much longer.